Knitting Scheme Development - From Art to Science
Abstract
Commercial knitting scheme on single knit fully fashion jersey fabric is studied by knitting with different fibres (wool, acrylic, cashmere, pima cotton and combed cotton) under three different knitting tensions (tight, normal and loose tension). Results show that different materials would affect the final fabric dimensions in terms of knitting tension and machine gauge. Tightness factor is a good indicator to predict different machine gauge and fabric loop length. Construction of knitting scheme must take into account of textile fibres and knitting tensions.
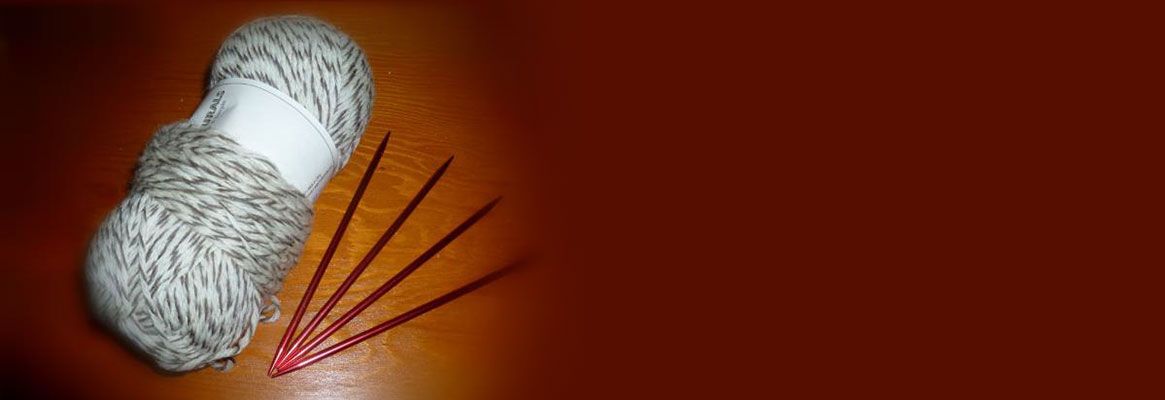
1. Introduction and Background
Flat knitting is one of the most important technological inventions for knitwear design and production that has gone through a lot of changes over time (1, 2, and 3). When comparing the primary flat knitting using jacquard steel for needle selection with the state-of-the art machine for integral shape knitwear, one can readily realize the amount of breakthroughs in this progression. The huge improvement in the efficiency of loop transfer has replaced the flat bed purl knitting machine with double hooked latch needles. The knitting production process evolved from cut-and-sewn piece goods knitting to fully fashion shaped knitting, and finally to integral shape knitting. The latest machine has completely eliminated the cutting and linking processes and put things together in one single operation.
This paper was originally presented at The 86th Textile Institute World Conference held on 18-21 November, 2008 at Hong Kong.
About the Author:
Arkin Ng is associated with Natalia Fashion Ltd, Hong Kong
Jimmy K.C. Lam is associated with the Hong Kong Polytechnic University, Hong Kong