Surface modification of PBO fiber by electrostatic discharge for composites
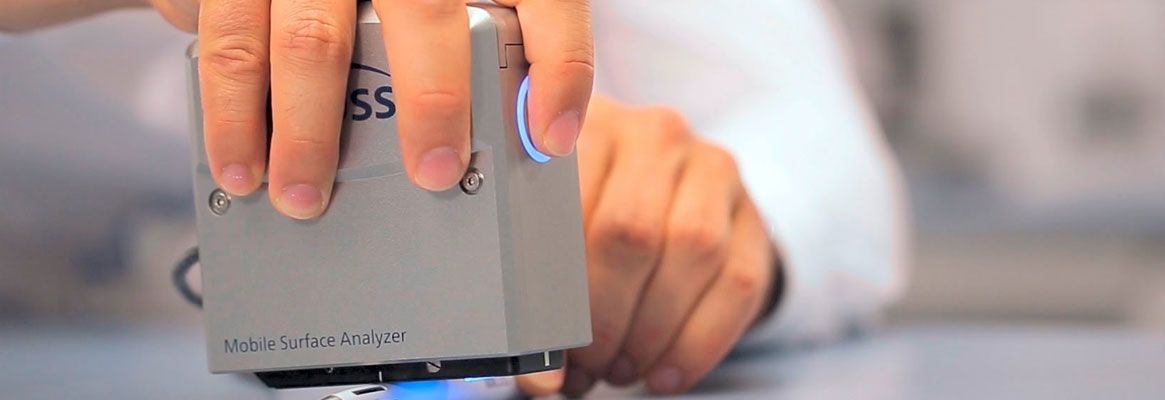
Abstract
Purpose: PBO fibers provide great potential applications as reinforcement fibers for advanced composites due to the excellent thermal resistance and specific stiffness and strength. However, the interfacial adhesion between reinforcing fiber and polymer matrix in a composite system is a primary factor for the stress transfer from matrix to fiber. In this paper, the effects of surface treatment on the modification of PBO fiber and its composite materials have been investigated using electrostatic discharge under atmospheric pressure. The surface treatment process has been designed to improve fiber/matrix interfacial bonding quality while providing minimum alteration to the bulk characteristics of the reinforcement fiber.
Design/methodology/approach: Both as-spun (AS) and high-modulus (HM) PBO fibers were surface treated and characterized in this study. The characterization techniques included scanning electron microscopy, MTS tensile tester, dynamic contact angle analysis system and microbond pull-out tests.
Findings: The results showed that PBO fibers exhibited -10% reduction in tensile strength after the proposed treatment process. The AS fiber surface free energy could be increased from 49.90 mJ/m2to 65.42 mJ/m2 (+31%) and the HM fiber surface free energy could be increased from 46.20 mJ/m2 to 65.36 mJ/m2 (+41%). The interfacial shear strength between PBO fiber and the epoxy matrix was improved to 41.6 MPa (+20%) for AS fiber system, and it improved to 40.1 MPa (+23%) for HM fiber system. The composite failure mode also shifted from fiber/matrix interface adhesive failure to partly cohesive failure.
Research limitations/implications: The composite interfacial shear strength was improved through the increased surface free energy of PBO fiber. The more cohesive failure mode allowed more energy to be dissipated during failure.
Originality/value: The proposed electrostatic discharge treatment process could improve the surface characteristics of PBO fiber and the applications in advanced composites.
Keywords: Composites; Surface treatment; Surface free energy; Interfacial shear strength
1. Introduction
In the continued quest for high performance, high temperature and lightweight materials, the development of poly (1,4-phenylene-cis-benzobisoxazole) or PBO polymeric material has been a significant step [1-3]. The specific tensile stiffness, specific tensile strength, and thermal and environmental stability of PBO fiber surpass those of many other materials.
PBO belongs to the new class of high performance rigid-rod PBZ materials.The rigid rod main chain backbone structure provides excellent chemical resistance and ensures good tensile, impact and tribological properties under a wide range of conditions. The polymer is usually synthesized in strong acids and kept as a highly viscous dope for processing. Fiber spinning is done by a dry-jet wet-spinning technique that warrants a high degree of molecular chain orientation through an elongational flow. After coagulation in a suitable medium, the fiber is dried and heat-treated to set the structure. Several attempts have been carried out in pushing the mechanical properties towards the theoretical values based on molecular crystal structure [4]. So far, three PBO fiber grades have been available in the literatures, including as-spun (AS), high-modulus (HM), and an experimental grade fiber (HM+) that uses a non-aqueous coagulation method.
PBO fibers provide great potential applications as reinforcement fibers for advanced composites due to the excellent thermal resistance and specific stiffness and strength. However, the interfacial adhesion between reinforcing fiber and polymer matrix in a composite system is a primary factor for the stress transfer from matrix to fiber. Several surface treatment methods have been studied for the modification of fibers or polymers [5-7], including chemical treatment, plasma treatment, electrolytic oxidation, and coupling agents [8-10]. These surface treatment processes might generate chemical wastes that could pollute the environment, or have required a vacuum system that might be expensive to operate. It is therefore required to develop an environment-friendly process that can improve PBO fiber surface characteristics. The lower operation cost can be a plus.
In this paper, the effects of surface treatment on the modification of PBO fiber and its composite materials have been investigated using electrostatic discharge under atmospheric pressure. No chemical discharge was involved. The surface treatment process has been designed to improve fiber/matrix interfacial bonding quality while providing minimum alteration to the bulk characteristics of the reinforcement fiber. Both as-spun (AS) and high-modulus (HM) PBO fibers were surface treated and characterized in this study. The fiber surface morphology was examined by scanning electron microscopy. The corresponding change in fiber tensile strength was measured by MTS tensile testing machine using a cardboard sample frame. The surface free energy was quantified using a dynamic contact angle analysis system. In addition, the interfacial adhesion properties of the PBO fiber reinforced epoxy composites were studied by microbond pull-out tests. In addition, the composite failure mode would be discussed.
2. Experimental
2.1 Materials
The PBO fiber samples were cleaned and dried before being used in the electrostatic discharge treatment study. Both AS and HM PBO fibers were received from Toyobo Co. Ltd, Japan. The surface treatment of PBO fiber samples were carried out using SC-PM5 electrostatic discharge system (Sien Chun Electric, Taiwan). Two different operating voltages were studied at room temperature and atmospheric pressure: 5 kV and 10 kV. Much higher voltage would create unstable discharge that resulted sparks and could damage the fiber samples. The distance between the discharge electrode and the samples was about 1.5 cm. The PBO fiber sample was fed through at a linear velocity of 1 m/min while the discharge electrode system was kept stationary.
2.2 Analysis of PBO fibers
The surface morphology of PBO fiber both before and after the electrostatic discharge treatment was examined by scanning electron microscopy. The corresponding tensile strength properties of the fiber samples were analyzed by MTS tensile testing machine at room temperature. Each monofilament sample was mounted across a cardboard sample frame using a room temperature curing adhesive according to ASTM D3379-75. A gauge length of 10 mm at a crosshead speed of 1 mm/min was used. The tensile strength was then calculated from the ultimate load divided by the cross-sectional area.
The surface free energy of PBO fiber was analyzed from the measured contact angles between each sample and five different liquid contact media, including n-hexadecane, dimethyl sulfoxide (DMSO), ethylene glycol (EG), formamide and water. A Cahn DCA-322 dynamic contact angle analysis system was used at 25C. The surface free energy γ was calculated by an extrapolation method [11]. The dispersive componentγd (α2) was derived from the intercept and the polar componentγp (β2) was from the slope data.
2.3 Characterization of PBO Composites
The effects of electrostatic discharge modification on the interfacial adhesion properties between PBO fiber and epoxy matrix were studied by microbond pull-out tests. The Epon 828 type epoxy was premixed with a hardener and delivered to PBO fiber using a syringe. The cured epoxy was then debonded in shear from PBO fiber by the jaws of a microvice. The microbond specimens were pulled by MTS tensile testing machine at room temperature at a crosshead speed of 0.5 mm/min [12].
The apparent interfacial shear strength (IFSS) was calculated from t= F/pDL. Here, F is the pull-out load, D is the diameter of the fiber, and L is the embedded length. In addition, some unidirectional PBO fiber reinforced epoxy model composites were prepared from fiber strands. These samples were fractured to reveal the interfacial adhesion bonding quality by the examination using scanning electron microscopy.
3. Results and discussion
3.1 PBO Fibers
The surface morphology of the treated PBO fibers has been examined by scanning electron microscopy and is shown in Figures 1. The surface displayed some scars from the electrostatic treatment effects also discharge treatment. It seemed that a thin layer of oxidized substance has been deposited on the surface. The surface appeared to be still uniform. The degree of surface modification increased with the applied discharge voltage. However, when the applied discharge voltage was above 20 kV, the treatment process could have seriously damaged the fiber structure integrity.
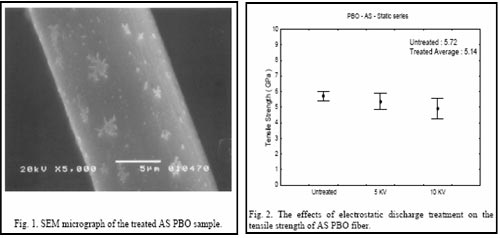
The effects of electrostatic discharge treatment process on the tensile strength properties of PBO fibers are shown in Figure 2. The results showed that the untreated AS fiber had a tensile strength of 5.72 GPa while the treated fibers showed an average value of 5.14 GPa. This represented a reduction in strength by 10%. Therefore, PBO fibers exhibited limited reduction in their tensile strengths after the suitable electrostatic discharge treatment process.
The fiber surface free energy characteristics were also derived from a dynamic contact angle analysis system and the measured contact angles are shown in Table 1. The measured contact angles were decreased along the treatment process. This suggested a better wettability for composite processing. The calculated surface free energy components are listed in Table 2.
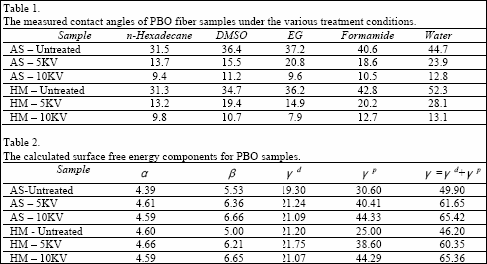
The untreated AS-UT sample showed a total surface free energy of 49.9 mJ/m2 while the value increased with the discharge voltage. The total surface free energy of AS-10kV was improved by +31% to 65.42 mJ/m2. In addition, the polar components of the surface free energy increased much more than the dispersive components.
3.2 PBO composites
The effects of electrostatic discharge treatment on PBO fiber reinforced epoxy composites were also studied. The measured apparent interfacial shear strength results of the AS PBO fiber model composites are shown in Figure 3. Shear debonding was observed throughout the examination. The untreated AS-UT PBO system exhibited a lower value of 34.7 MPa. The interfacial shear strength was increased to 41.6 MPa for the AS-10kV sample. This represented an improvement by +20%. The trend has been in accordance with the results in fiber surface free energy analysis. For the HM PBO epoxy model composite systems, the interfacial shear strength was the lowest at only 32.5 MPa for the untreated HM-UT sample. After the proposed electrostatic discharge treatment experiment at 10 kV, the HM sample showed an improvement of +23% in its interfacial shear strength to 40.1 MPa.
The treated fiber system showed significant amount of epoxy resin adhered to PBO fiber surface (not shown). The failure mode has changed from adhesive failure to partly cohesive failure after the electrostatic discharge treatment. This explained the modification improvement results in the corresponding apparent interfacial shear strength data in the microbond tests.

4. Conclusions
The effects of electrostatic discharge treatment on PBO fiber and the composites have been investigated. Both AS and HM grade PBO fibers were surface treated and characterized in this study. The results showed that PBO fibers exhibited -10% reduction in tensile strength after the treatment process. The decrease in contact angle and the increase in fiber surface free energy could help composite processing and the resulting interfacial shear strength. The AS fiber surface free energy could be increased from 49.90 mJ/m2 to 65.42 mJ/m2 and the HM fiber surface free energy could be increased from 46.20 mJ/m2 to 65.36 mJ/m2. The interfacial shear strength between PBO fiber and the epoxy matrix was improved to 41.6 MPa for AS fiber system, and it improved to 40.1 MPa for HM fiber system. The composite failure mode also changed from fiber/matrix interface adhesive failure to partly cohesive failure. AS and HM PBO showed similar trends.
References
1) S. Bourbigot and X. Flambard, Heat resistance and flammability of high performance fibres: A review, Fire and Materials, 26 (2002) 155-168.
2) F. Larsson and L. Svensson, Carbon, polyethylene and PBO hybrid fibre composites for structural lightweight armour, Composites Part A: Applied Science and Manufacturing, 33 (2002) 221-231.
3) G. M. Wu and Y. T. Shyng, Surface modification and interfacial adhesion of rigid rod PBO fibre by methanesulfonic acid treatment, Composites Part A: Applied Science and Manufacturing, 35 (2004) 1291-1300.
4) R. J. Davies, M. A. Montes-Moran, C. Riekel and R. J. Young, Single fibre deformation studies of poly(p- phenylene benzobisoxazole) fibres: Part I. Dertermination of crystal modulus, Journal of Materials Science, 36 (2001) 3079-3087.
5) E. David, A. Lazar and A. Armeanu, Surface modification of polytetrafluoroethylene for adhesive bonding, Journal of Materials Processing Technology, 157 (2004) 284-289.
6) D. Sun and G. K. Stylios, Fabric surface properties affected by low temperature plasma treatment, Journal of Materials Processing Technology, 173 (2006) 172-177.
7) L. Carrino, G. Moroni and W. Polini, Cold plasma treatment of polypropylene surface: a study on wettability and adhesion, Journal of Materials Processing Technology, 121, (2002) 373-382.
8) G. S. Sheu, S. S. Shyu, Surface properties and interfacial adhesion studies of aramid fibres modified by gas plasmas, Composites Science and Technology, 52 (1994) 489-497.
9) L. Szazdi, J. Gulyas, B. Pukanszky, Electrochemical oxidation of carbon fibres: adsorption of the electrolyte and its effect on interfacial adhesion, Composites Part A: Applied Science and Manufacturing, 33 (2002) 1361-1365.
10) G. M. Wu, C. H. Hung, J. H. You and S. J. Liu, Surface modification of reinforcement fibers for composites by acid treatments, Journal of Polymer Research, 11 (2004) 31-36.
11) G. M. Wu, J. M. Schultz, D. J. Hodge, F. N. Cogswell, Effects of treatment on the surface composition and energy of carbon fibers, Polymer Composites, 16 (1995) 284-287.
12) R. Zulkifli, L. K. Fatt, C. H. Azhari and J. Sahari, Interlaminar fracture properties of fibre reinforced natural rubber/polypropylene composites, Journal of Materials Processing Technology, 128 (2002) 33-37.
About the Authors:
The authors are associated with Advanced Materials Laboratory and Institute of Electro-Optical Engineering, Chang Gung University, Taiwan R.O.C.